When comparing malleable cast iron and ductile iron, it's important to understand that while both are types of cast iron, they have distinct properties and are suited for different applications. Here's a detailed comparison:
1. Material Composition and Structure
Malleable Cast Iron:
Composition: Malleable cast iron is created by heat-treating white cast iron, which contains carbon in the form of iron carbide (Fe3C). The heat treatment, known as annealing, breaks down the iron carbide, allowing carbon to form graphite in a nodular or rosette form.
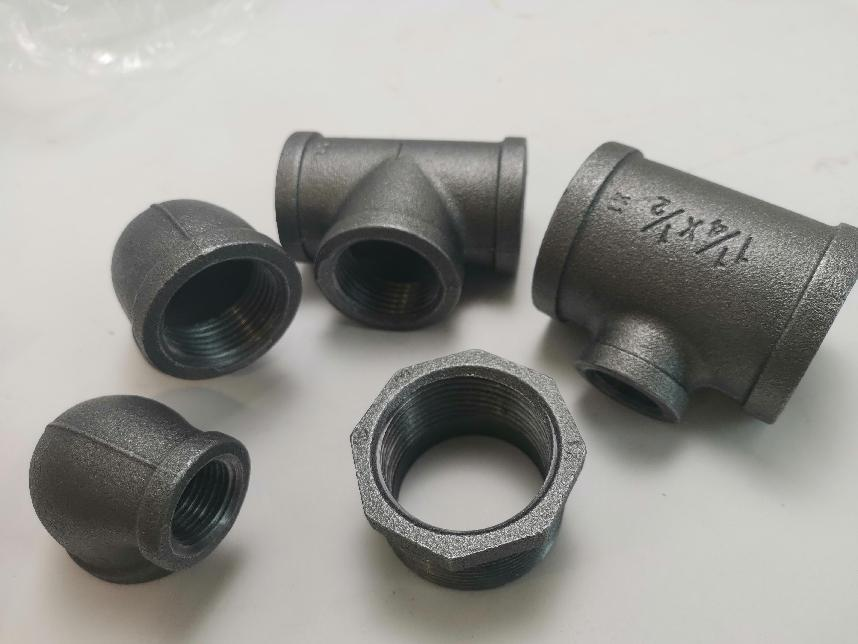
Structure: The annealing process changes the microstructure of the iron, resulting in small, irregularly shaped graphite particles. This structure provides the material with some ductility and toughness, making it less brittle than traditional cast iron.
Ductile Iron:
Composition: Ductile iron, also known as nodular or spheroidal graphite iron, is produced by adding nodulizing elements such as magnesium or cerium to molten iron before casting. These elements cause the carbon to form as spheroidal (round) graphite nodules.
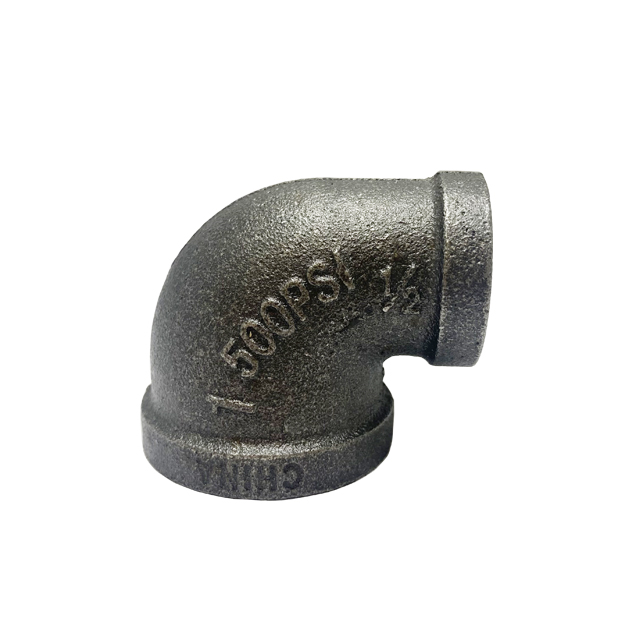
Structure: The spherical graphite structure in ductile iron enhances its ductility and impact resistance, giving it superior mechanical properties compared to malleable iron.
2. Mechanical Properties
Malleable Cast Iron:
Tensile Strength: Malleable cast iron has a moderate tensile strength, typically ranging from 350 to 450 MPa (megapascals).
Ductility: It has reasonable ductility, which allows it to bend or deform under stress without cracking. This makes it suitable for applications where some flexibility is required.
Impact Resistance: While it is tougher than traditional cast iron, malleable cast iron is less impact-resistant compared to ductile iron.
Ductile Iron:
Tensile Strength: Ductile iron has a higher tensile strength, often ranging from 400 to 800 MPa, depending on the grade and heat treatment.
Ductility: It is highly ductile, with elongation percentages typically between 10% and 20%, meaning it can stretch significantly before fracturing.
Impact Resistance: Ductile iron is known for its excellent impact resistance, making it ideal for applications subject to dynamic loading or high stress.
3. Applications
Malleable Cast Iron:
Common Uses: Malleable cast iron is often used in smaller, more intricate castings such as pipe fittings, brackets, and hardware where moderate strength and some flexibility are required.
Typical Environments: It is commonly used in plumbing, gas piping, and light industrial applications. The material's ability to absorb shock and vibrations makes it suitable for installations involving mechanical movements or thermal expansion.
Ductile Iron:
Common Uses: Due to its superior strength and toughness, ductile iron is used in larger and more demanding applications such as automotive components (e.g., crankshafts, gears), heavy-duty pipe systems, and structural parts in construction.
Typical Environments: Ductile iron is ideal for use in high-pressure pipelines, water and sewage systems, and situations where components are subjected to significant mechanical stress or wear.
Conclusion
Malleable iron and ductile iron are not the same. They are distinct types of cast iron with different properties and applications.
Malleable iron is suitable for less demanding applications where cost-effectiveness and moderate mechanical properties are sufficient.
In contrast, ductile iron is chosen for more challenging environments where higher strength, ductility, and impact resistance are required.
Post time: Aug-24-2024